Digital Roadmap Development
Polaris Automation's consultative approach helps manufacturers build and navigate their digital transformation strategy with an unbiased perspective and practical recommendations informed by decades of real-world manufacturing experience. Our approach provides focus, validates each step of your manufacturing process, and helps you create an environment of continuous improvement.
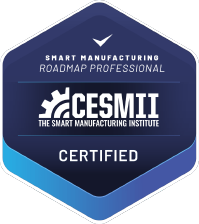
A process driven by data gets results faster
Smart Manufacturing Acceleration Framework:
1. Explore
Our process begins with an introductory conversation to explain the value of our consultative approach. We attend events, review competitors, explore options, address challenges, share success stories, seek demonstrations and pilot technology.2. Assess
We engage front-line personnel to review process data and business goals to understand your organization and team. We share insights gained and come to consensus about the current state of operations: competitiveness, market readiness, people, process and technology. This helps determine our areas of focus.3. Focus
We conduct deep-dive interviews and analyze insights to identify performance gaps and present opportunities such as business drivers and value proposition. Focusing on what will yield the greatest value in the least amount of time, we come to an agreement about the future state of your operations.4. Roadmap
We develop business objectives and programs, identify business drivers and key milestones, define project scope, and prioritize initiatives…creating a literal roadmap to achieve the goals we've identified and agreed upon together.5. Execute & Sustain
We execute the roadmap and achieve the first benchmark. The focus is on visibility and understanding what the data is communicating so improvements are sustainable. Using data to identify areas for improvement, we execute the plan in support of what drives your business - bringing the group to consensus about new benchmarks to pursue.6. Validate
The contextualized data speaks for itself as your operation achieves greater efficiency. We validate success through business value, impact, and timelines. Every success creates opportunities for further improvement - expansion is key. What we learn is applied more efficiently to the next process. Then the next process.Frequently Asked Questions
- What is Smart Manufacturing?
Smart Manufacturing leverages technology to tie your entire business operation together - allowing you to enhance quality, efficiency and productivity to meet your customers' demands like never before.
- What are the key technologies involved in Smart Manufacturing?
The core technologies that enable Smart Manufacturing include:
- Internet of Things (IoT): Sensors and connected devices gather and exchange real-time data from machinery and production processes.
- Artificial Intelligence (AI) and Machine Learning (ML): For predictive maintenance, quality control, and optimization of operations.
- Data and Analytics: To add context to data collected from various sources, providing insights into improving efficiency and decision-making.
- Automation and Robotics: Used to increase speed, precision, and safety in manufacturing processes.
- Cloud Computing: For data storage, processing, and sharing across multiple platforms.
- Digital Twins: Virtual replicas of physical systems used for simulation and predictive analysis.
- What are the benefits of adopting Smart Manufacturing?
Benefits of Smart Manufacturing include:
- Increased Efficiency: Real-time data enables quick adjustments, reducing downtime and bottlenecks.
- Cost Savings: By improving resource management and reducing waste, energy costs, and manual errors.
- Flexibility and Customization: Easier to pivot production processes to meet demand for customized products.
- Improved Product Quality: Automated monitoring ensures consistent quality control.
- Predictive Maintenance: Machine learning can predict equipment failures before they happen, reducing unexpected downtime.
- What is the role of data in Smart Manufacturing?
Challenges include:
- Initial Cost: Investment in technology and infrastructure.
- Integration Complexity: Existing legacy systems may be difficult to integrate with new digital technologies. Finding th right partner is critical.
- Cybersecurity Risks: Increased connectivity can expose manufacturers to cybersecurity threats. Implementing strong cybersecurity measures, like encryption, secure network architectures, and regular security audits, is essential to prevent these risks.
- Skill Gaps: Requires new technical expertise that may not be readily available within the current workforce.
- How does Smart Manufacturing impact the workforce?
Manufacturers can start by:
- Assessing current capabilities and identifying areas where smart technologies can bring the most value.
- Starting with pilot projects to introduce specific technologies (e.g., IoT sensors or predictive maintenance tools).
- Investing in workforce training to ensure employees are equipped to work with new systems.
- Collaborating with technology providers to design and implement customized solutions.
- What are the challenges of implementing Smart Manufacturing?
Challenges include:
- Initial Cost: Investment in technology and infrastructure.
- Integration Complexity: Existing legacy systems may be difficult to integrate with new digital technologies. Finding th right partner is critical.
- Cybersecurity Risks: Increased connectivity can expose manufacturers to cybersecurity threats. Implementing strong cybersecurity measures, like encryption, secure network architectures, and regular security audits, is essential to prevent these risks.
- Skill Gaps: Requires new technical expertise that may not be readily available within the current workforce.
- How can a manufacturer begin transitioning to Smart Manufacturing?
Manufacturers can start by:
- Assessing current capabilities and identifying areas where smart technologies can bring the most value.
- Starting with pilot projects to introduce specific technologies (e.g., IoT sensors or predictive maintenance tools).
- Investing in workforce training to ensure employees are equipped to work with new systems.
- Collaborating with technology providers to design and implement customized solutions.
- What is the role of cybersecurity in Smart Manufacturing?
As manufacturing systems become more connected, cybersecurity becomes a crucial factor. Smart Manufacturing systems must be protected from cyber threats such as hacking, data breaches, and system disruptions. Implementing strong cybersecurity measures, like encryption, secure network architectures, and regular security audits, is essential to prevent these risks.
- How does Smart Manufacturing contribute to sustainability?
Smart Manufacturing supports sustainability through:
- Energy Efficiency: Real-time monitoring of energy usage allows for reductions in power consumption.
- Waste Reduction: Optimized processes and predictive maintenance reduce material waste and product defects.
- Resource Management: AI can optimize resource use, making production more sustainable and reducing environmental impact.
- What is the difference between Smart Manufacturing and Industry 4.0?
Industry 4.0 refers to the broader concept of the fourth industrial revolution, which includes the digital transformation of industries through technologies like IoT, AI, and automation. Smart Manufacturing is the practical application of these technologies specifically within the manufacturing sector to improve production efficiency, flexibility, and innovation.
- How can manufacturers ensure scalability with Smart Manufacturing technologies?
Scalability can be ensured by:
- Choosing flexible and modular technologies that can be expanded as needed.
- Using cloud-based solutions to handle growing data storage and processing needs.
- Developing a long-term strategy that accounts for both short-term gains and future growth.
- Implementing standards-based systems to ensure compatibility across new and existing platforms.
- Are there any specific industries where Smart Manufacturing is more applicable?
Smart Manufacturing is applicable across a wide range of industries, including:
- Automotive: For automated assembly lines and predictive maintenance.
- Aerospace: For precision manufacturing and real-time quality monitoring.
- Pharmaceuticals: To ensure compliance with strict regulatory standards and optimize production processes.
- Consumer Goods: For agile manufacturing and personalized product offerings.
- Electronics: To maintain high-quality standards and quick production cycles.
- How does Smart Manufacturing impact supply chain management?
Smart Manufacturing improves supply chain management by:
- Real-time tracking: Sensors and IoT devices provide visibility into the movement of raw materials and products.
- Improved forecasting: Data analytics predict demand trends, helping manufacturers manage inventory effectively.
- Enhanced collaboration: Digital platforms enable better coordination with suppliers and distributors.